技術レポート1
世界で初めてテーラードブランクのリヤビームを開発!
本田技研工業殿より
開発賞を受賞
テーラードブランクリヤビームは
ココがスゴイ!
ヨロズの高い開発力と生産技術力により、質量の軽減と剛性の向上を実現したテーラードブランクリヤビームの特長を紹介します。
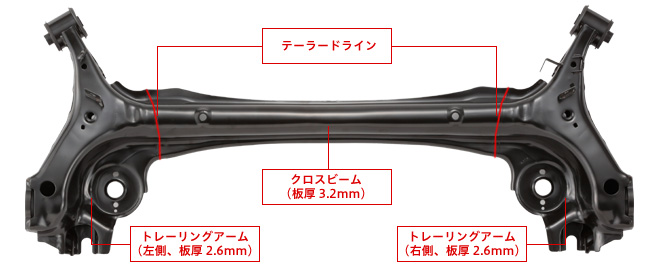
2011年、ヨロズは従来構造とはまったく異なるテーラードブランクリヤビームを開発しました。
HONDAのN-BOXに搭載されたこのリヤビームは、トレーリングアームとクロスビームの接合に世界で初めてテーラードブランク工法を採用し、質量の軽減と剛性の向上を実現しました。
ヨロズの開発力と生産技術力により完成させた、テーラードブランクリヤビームの魅力を紹介します。
特長1:構造
一体構造化で軽量かつ高剛性を実現!
テーラードブランクリヤビームは板厚が異なるトレーリングアームとクロスビームをテーラードブランクで一体化することで形状連続性を高め接合部の局部変形と応力集中を抑えながら、部品同士の溶接重ね代や溶接ビード自体の質量軽減を図りました。また、スプリングシートも一体化し補強部材として利用することで、タイヤからの力を効率よくクロスビームに伝達させることができ左右剛性の向上も実現しました。
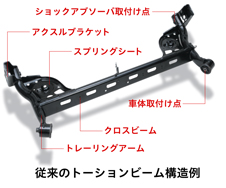
従来構造の課題
従来の構造は、トレーリングアーム、クロスビーム、スプリングシートなどの各機能部位ごとに構成部品を分け異なる板厚を設定し、アーク溶接で接合しています。接合部は局所変形が起こり応力も集中するため、剛性と耐久性の確保に接合長さの延長や補強部材の追加が必要となり、質量増の傾向があります。
特長2:接合
母材と同等レベルの疲労強度と成形性を接合部で実現!
テーラードブランクの接合にはプラズマ溶接という接合技術を使用しています。この接合技術は、厚さの異なる鋼板を直接溶かして滑らかに接合でするので、アーク溶接のような溶接ビード止端部とルート部への応力集中の発生がなく、母材と同等レベルの高い疲労強度を得ることができます。
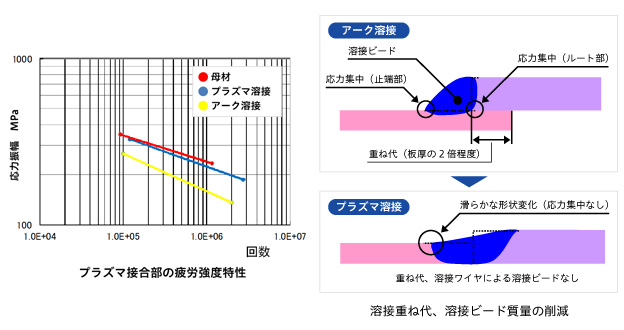
ただし、テーラードブランクをプレス成形する場合、差厚部の段差や硬度の不均一性などによる成形割れが懸念されるため、ロバストなプレス成形性を確保したプラズマ溶接条件の見極めが必要となります。今回、溶接条件の設定に実験計画法、成形性の評価に引張り試験の荷重-変位線図を用いることで、溶接条件を最適化し、成形の安定化を実現しました。なお、ロバストなプレス成形性を確保した良いプラズマ溶接の条件は、引張り試験の荷重-変位線図が母材と同じ特性を示し、溶接部から破断することはなく薄板部が破断する条件を良い条件としました。
プラズマ溶接の溶接条件最適化
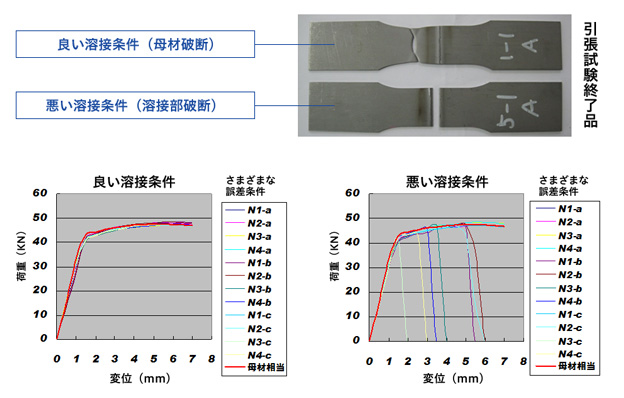