技術レポート2
日産GT-Rの時速300kmを超える高速走行を支えるサスペンションメンバー
複雑な6点マウント方式パイプフレーム構造で高精度を実現!
ヨロズの最新測定技術を駆使した、金型、組立治具への高いフィードバック技術を紹介します。
ポイント:精度
非接触3次元測定機を用いたフィードバック技術で従来の2/3※の
寸法公差域を実現!
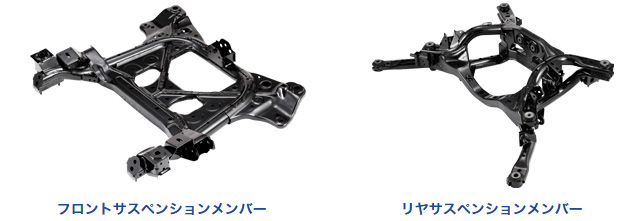
※走行性能に関わる箇所の寸法のみです。
-
フロントサスペンションメンバーは基本骨格となるU字パイプにボディやリンク類の取り付け点が平面的に配置された構造。構成部品は高低差が小さく簡素な形状のため、プレス成形での精度確保は容易。しかし、ほぼ全ての構成部品が接続されるU字パイプの厚さは1.8mmと薄く、アーク溶接の熱でパイプが歪むため、溶接の条件や順序で各取り付け点寸法は大きく変動します。今回、非接触3次元測定機で加工後の形状変動を定量的に掴み、蓄積したノウハウを効率よく活かすことで高精度な製品玉成を従来よりも短期間で実現しました。
-
リヤサスペンションメンバーは上下2段の立体的な3次元曲げパイプを左右に配置し、前後にクロスメンバーを橋渡しする非常に複雑な構造。上下2段のパイプ曲面に前後のクロスを溶接するだけでも困難ですが、パイプの厚さが1.6mmと薄く、溶接の熱歪により部品の合わせ部やボディやリンク類の取り付け点寸法が大きく変動するため、精度と品質の確保は困難を極めます。今回、試作段階から非接触3次元測定機による測定を重ね、設計値と加工後品の差を定量的にプレス金型やアーク溶接治具にフィードバックすることで高い精度の確保を実現しまた。
非接触3次元測定機とは
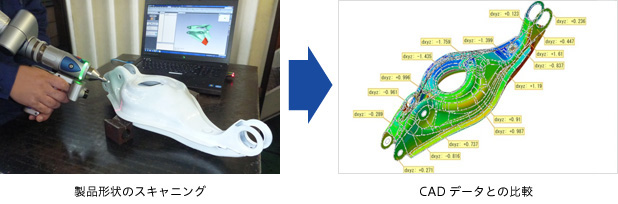
製品をレーザーや光などを用いて測定し、3次元データ化する測定機であり、製品が設計値どおりに作られているかなどを検査することができます。