Technical Releases2
High-precision suspension members for stable driving on a straight course even at 300 km/h
High precision achieved through a complex pipe frame structure with a 6-point mount system!
Learn about the sophisticated feedback technique that mobilizes Yorozu’s latest measurement technology to feed measurements to dies and assembly jigs.
Key point: Precision
2/3 of the previous dimensional tolerance range achieved through feedback technology that deploys a non-contact 3-dimensional measuring system!
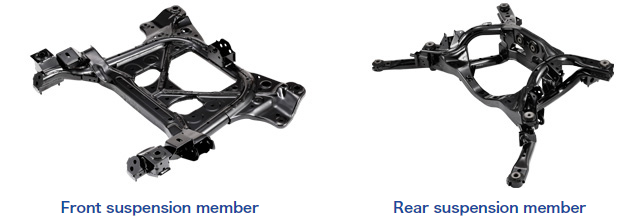
-
In the structure of the front suspension member, the body and link attachment points are positioned on the same plane and laid out on a U-shaped pipe that serves as the basic frame. Its constituent parts have small differences in height and simple shapes, so it is easy to ensure their precision at the press molding stage. However, the thickness of the U-shaped pipe to which almost all the constituent parts are joined is only 1.8 mm, and the heat emitted during arc welding causes the pipe to become deformed. This means that the dimensions of the attachment points vary greatly depending on the welding conditions and sequence. Nevertheless, using our non-contact 3-dimensional measuring system to quantitatively assess shape variations after machining and effectively applying our accumulated knowledge, it now takes less time than ever to complete the product improvement process.
-
The rear suspension member has a very complex structure in which the top and bottom dual layer 3-dimensionally bent pipes are positioned at the left and right to bridge the cross members at the front and back. Even welding the front and back cross members to the top and bottom dual layer pipe curves alone is challenging. Moreover, the pipes are only 1.6 mm thick, and the dimensions of the areas where parts are joined together and of the body and link attachment points vary greatly due to the thermal strain of welding. This makes the task of ensuring precision and quality extremely difficult. Nevertheless, we successfully ensure a high level of precision through repeated measurements using our non-contact 3-dimensional measuring system right from the development stage, and quantitative feedback of any disparities between the design values and post-machined parts to the press mold and arc welding jigs .
What is a non-contact 3-dimensional measuring system?
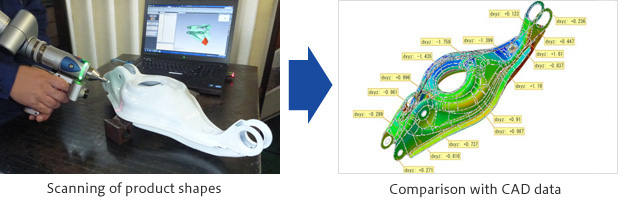
Our measuring system uses lasers, light, and other means to measure products and turn those measurements into 3-dimensional data. This makes it possible to inspect whether products have been created in line with their design values.